Industrial Wireless Sensors for Business
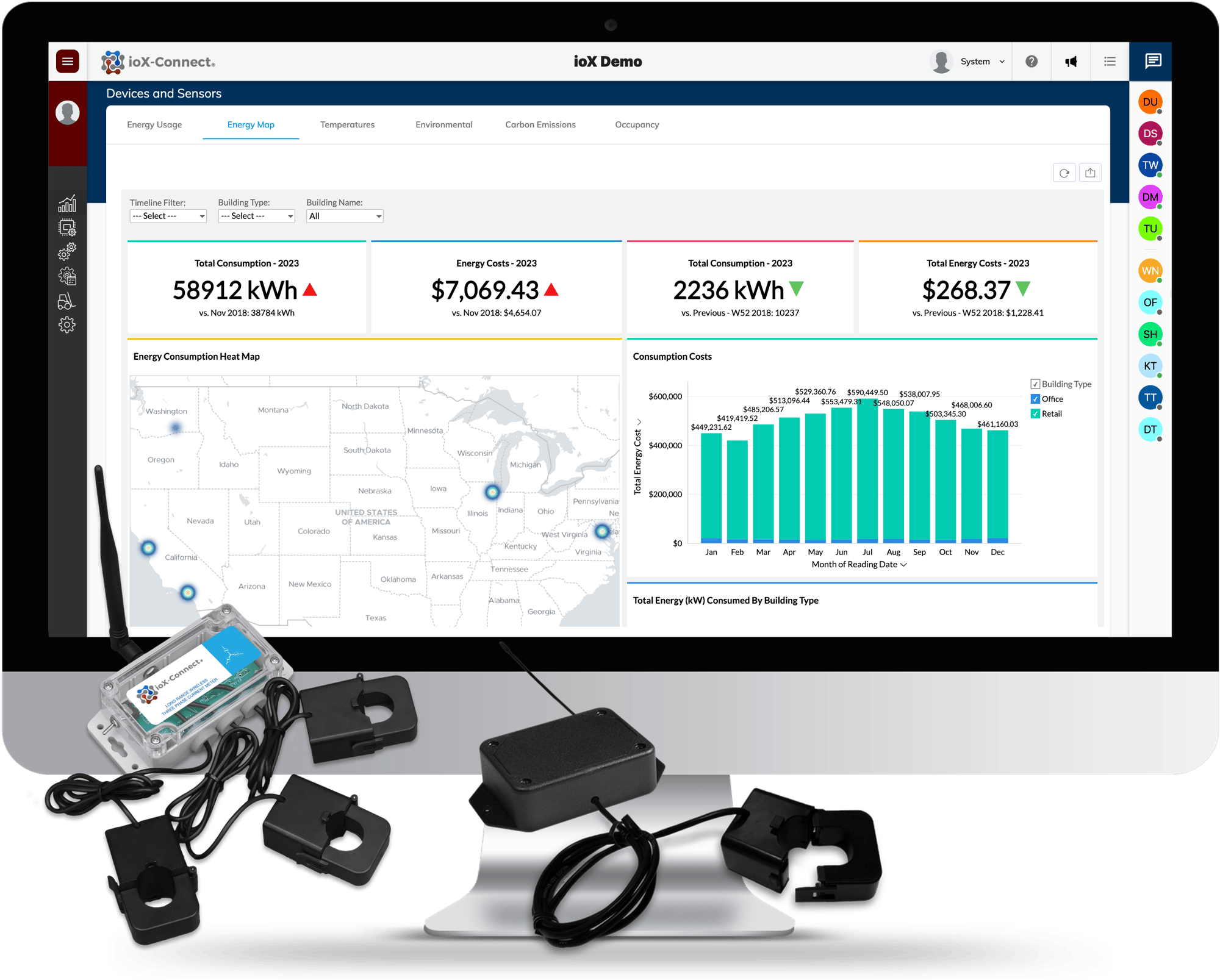
Empower Your Business with ioX-Connect Industrial Wireless Sensors
Welcome to ioX-Connect, your go-to resource for cutting-edge wireless industrial sensors. Our mission is to provide innovative solutions that enhance operational efficiency, safety, and reliability across various industrial sectors. This page aims to offer comprehensive insights into our range of wireless industrial sensors, addressing key questions and showcasing why ioX-Connect is a leader in this space.
Key Features of ioX-Connect Wireless Industrial Sensors
- Extended Wireless Range: Up to 2,000+ feet through 18+ walls.
- Frequency-Hopping Spread Spectrum (FHSS): Ensures robust and interference-free communication.
- Best-in-Class Power Management: Longer battery life for continuous monitoring.
- Advanced Security: Encrypt-RF® Security ensures data integrity and confidentiality.
- Data Logging: Sensors log 2000 to 4000 readings if the gateway connection is lost.
- Automatic Firmware Updates: Over-the-air updates to keep sensors up-to-date.
ioX-Connect Wireless Industrial Sensors
If you have any questions regarding any of our industrial sensor range, please contact us at: sales@iox-connect.com
Key Benefits of ioX-Connect Wireless Industrial Sensors
Choosing ioX-Connect wireless industrial sensors means opting for a solution that delivers unparalleled benefits across various dimensions of your business operations. Here’s why investing in our wireless sensors is a smart move
Effortless Installation and Maintenance
One of the most significant advantages of wireless sensors is the ease of installation. Unlike wired systems that require extensive cabling, our wireless sensors can be set up quickly and effortlessly, even in remote or hard-to-reach areas. This translates to reduced installation costs and minimal disruption to your operations. Additionally, maintenance is straightforward, with fewer physical components to manage and no cables to degrade over time.
Scalability and Flexibility
As your business grows, so do your monitoring needs. ioX-Connect wireless sensors offer exceptional scalability, allowing you to easily expand your sensor network as required. This flexibility means you can adapt to changing operational demands without the need for significant infrastructure changes. Whether you need to add a few sensors or hundreds, our system can accommodate your needs seamlessly.
Real-Time Data and Enhanced Decision Making
Wireless industrial sensors provide real-time data transmission, giving you instant access to critical information. This immediacy allows for quicker decision-making and more responsive management of your operations. By having up-to-the-minute data, you can identify issues before they escalate, optimize processes, and improve overall efficiency.
Cost Efficiency and ROI
Investing in industrial wireless sensors from ioX-Connect is not just about the initial purchase but about long-term savings and return on investment. Reduced installation and maintenance costs, coupled with the ability to prevent costly downtime and inefficiencies, make wireless sensors a cost-effective solution. Moreover, the ability to integrate with existing systems and infrastructure minimizes the need for additional investments.
What role do wireless sensors play in supporting predictive maintenance?
The Role of Wireless Sensors in Predictive Maintenance
Wireless sensors are revolutionizing predictive maintenance in industrial settings, offering a smarter way to manage machinery and equipment. These devices gather real-time data from various components of the machinery, ensuring that manufacturers can maintain optimal efficiency and minimize unexpected breakdowns.
Enhancing Real-Time Monitoring
Wireless sensors excel at providing instantaneous updates on equipment status. They detect changes in conditions, enabling swift identification of potential problems. This real-time feedback loop ensures that issues can be addressed before they escalate into major faults, thereby supporting seamless production operations.
Facilitating Predictive Insights
By continuously collecting and analyzing data across entire facilities, wireless sensors enable predictive maintenance strategies. This process involves forecasting equipment failures based on patterns and trends identified in the data. As a result, maintenance teams can address wear and tear or probable malfunctions proactively, rather than following a fixed schedule that might not accurately reflect the equipment's condition.
Reducing Downtime and Costs
The implementation of predictive maintenance driven by wireless sensors leads to reduced instances of unplanned downtime. By focusing on genuine issues and avoiding unnecessary maintenance, manufacturers can extend the lifespan of their machinery, significantly cutting down on operating costs.
In conclusion, wireless sensors are instrumental in reshaping maintenance strategies in industrial environments. They not only facilitate timely intervention but also enable smarter allocation of maintenance resources, fostering a more efficient and reliable manufacturing ecosystem.
How do wireless sensors facilitate predictive maintenance in manufacturing?
In the competitive realm of manufacturing, maintaining seamless operations is crucial. Wireless sensors have emerged as pivotal players in the predictive maintenance landscape, offering unparalleled advantages for production efficiency and equipment longevity.
Real-Time Data Collection
Wireless sensors excel in providing real-time insights, acting as vigilant sentinels over machinery. By delivering swift, accurate data, they help in promptly identifying potential errors or malfunctions. This immediate access to information allows manufacturers to address issues precisely when needed, preventing disruptions before they escalate.
Enhanced Monitoring Capabilities
These sensors continuously monitor equipment conditions across entire factories. By doing so, they gather critical data on performance metrics and environmental factors. Such comprehensive monitoring enables manufacturers to detect early signs of wear and tear, identifying anomalies that could signal impending failures.
Facilitating Predictive Maintenance
The core strength of wireless sensors lies in their ability to support predictive maintenance. Instead of relying on scheduled checks, manufacturers can base maintenance activities on actual equipment conditions. This approach minimizes unplanned downtime, extending machinery lifespan by addressing only those components that truly need attention.
Cost and Time Efficiency
Implementing predictive maintenance through wireless sensors reduces unnecessary expenditures on blanket maintenance routines. By focusing efforts on genuine issues, manufacturers save time and resources, optimizing the production line's overall efficiency.
Wireless sensors, by offering dynamic, detailed insights and enabling precise interventions, are transforming the way manufacturers approach equipment maintenance, ensuring operations remain smooth and cost-effective.
How do wireless sensors enhance safety in a manufacturing environment?
In the world of manufacturing, ensuring safety is paramount. Wireless sensors play a critical role in creating safer work environments by focusing on a few key areas:
-
Environmental Monitoring: These sensors constantly track conditions such as temperature, humidity, and air quality. By detecting potential hazards early, these devices allow for timely interventions, significantly reducing the chances of accidents.
-
Risk Mitigation: By integrating seamlessly into existing systems, wireless sensors can alert personnel when parameters deviate from set safety standards. This proactive communication helps in addressing issues before they escalate into dangerous situations.
-
Reducing Human Exposure: Wireless technology enables the use of automated systems in hazardous areas. By placing sensors and automated actuators in these zones, manufacturers can minimize human involvement, thereby reducing the potential for injury.
Through these applications, wireless sensors not only enhance operational efficiency but also cultivate a safer manufacturing environment.
What is the future potential of wireless sensors in IIoT manufacturing?
Wireless sensors are poised to revolutionize the Industrial Internet of Things (IIoT) landscape, thanks to their remarkable capabilities. Offering real-time data collection, these sensors are pivotal in optimizing processes and minimizing downtime. As manufacturing evolves, integrating wireless sensors will be key to maintaining a competitive edge.
Enhancing Operational Efficiency
- Real-Time Data: Wireless sensors provide instant insights, empowering manufacturers to make informed decisions swiftly.
- Predictive Maintenance: Identify potential issues before they escalate, reducing unplanned halts and maintenance costs.
- Operational Monitoring: These tools ensure systems run reliably, thereby boosting overall equipment effectiveness (OEE).
Driving the Shift in Manufacturing
In a data-driven era, the capacity to harness wireless sensor data is essential for staying agile. As demands fluctuate, these sensors enable manufacturers to adapt seamlessly and efficiently.
Long-Term Industry Benefits
- Increased Flexibility: Adapt processes based on dynamic data to meet production targets.
- Cost Efficiency: Cut costs by preemptively addressing machine failures and optimizing resource usage.
- Sustainability Goals: Achieve energy savings by monitoring and adjusting power use through precise data insights.
As IIoT technology continues to advance, wireless sensors will become even more vital for those looking to succeed in the complex manufacturing environment. Adopting these devices ensures sustainable growth and innovation in the industry.
What is the significance of factory floor-to-cloud connectivity in industry 4.0 and IIoT?
Factory floor-to-cloud connectivity plays a pivotal role in the evolution of Industry 4.0 and the Industrial Internet of Things (IIoT). It forms the essential link that enables seamless data transfer from machines and production lines to advanced cloud-based systems. This connectivity allows for real-time data collection, which is crucial for implementing data analytics, machine learning, and artificial intelligence.
By facilitating this data exchange, manufacturers can gain deeper insights into their operations, optimizing processes and maintaining high productivity levels. Industrial wireless sensors, part of the broader category of wireless devices, act as the critical enablers, constantly monitoring conditions and feeding valuable data to the cloud. This real-time data flow empowers smart factories to quickly detect and respond to any anomalies or dips in efficiency, ensuring that every part of the production process is running at its best.
In essence, factory floor-to-cloud connectivity is the backbone of modern manufacturing, enhancing operational agility and foresight, which are vital for meeting the demands of today's fast-paced industrial landscape.
How do vibration sensors help in monitoring equipment health?
Vibration sensors play a crucial role in maintaining the health of machinery. By capturing and analyzing vibrations, these sensors offer valuable insights into the operational status of various machine components.
Detecting Anomalies:
Vibrations often change when machinery experiences issues such as misalignments, unbalanced loads, or worn components. Vibration sensors detect these anomalies early, allowing for timely interventions before they lead to significant breakdowns.
Continuous Monitoring:
These sensors provide continuous data, facilitating ongoing monitoring of equipment. By comparing current vibration patterns with historical data, maintenance teams can identify deviations that might indicate emerging problems.
Preventive Maintenance:
One of the key benefits of vibration sensors is their ability to predict component failure. By spotting wear and tear early, these sensors enable the scheduling of maintenance activities, minimizing downtime and optimizing machine performance.
In essence, vibration sensors are vital for extending machinery lifespan and ensuring efficiency by preemptively addressing issues that could lead to costly repairs or operational halts.
In what ways are humidity sensors crucial for maintaining product quality and equipment availability?
Humidity sensors play a vital role in ensuring both product quality and equipment reliability across various industries. Here’s how:
Preserving Product Quality
-
Preventing Spoilage: In sectors like food production and pharmaceuticals, maintaining optimal humidity is essential. Excessive moisture can lead to spoilage or degradation, affecting the shelf life and safety of products.
-
Enhancing Material Performance: For materials such as wood, textiles, or electronics, incorrect humidity levels can cause warping, shrinkage, or malfunction. Sensors help maintain conditions that safeguard these materials.
Ensuring Equipment Reliability
-
Reducing Wear and Tear: High humidity can lead to rust and corrosion in machinery, reducing lifespan and increasing maintenance costs. Sensors alert you to undesirable conditions, allowing for timely adjustments.
-
Avoiding Downtime: By continuously monitoring humidity, these sensors help prevent unexpected equipment failures, thus minimizing production downtimes which can be costly.
Continuous Monitoring
Continuous feedback from humidity sensors allows for proactive management of environmental conditions. This ensures that both the production process and the end products are protected, wherever precision and reliability are crucial.
In essence, humidity sensors are indispensable in maintaining the delicate balance required for optimal production and equipment performance, safeguarding both the product and the process from the adverse effects of improper humidity levels.
Data Sheets:
OTHER DOCUMENTS:
Typical Use Cases and Applications of Industrial Wireless Sensors
Industrial wireless sensors play a crucial role in enhancing efficiency, safety, and productivity across a wide range of industries. Their flexibility, ease of deployment, and real-time data capabilities make them ideal for monitoring critical parameters and automating processes. Here are some typical use cases and applications:
1. Predictive Maintenance in Manufacturing
- Sensors Used: Vibration sensors, temperature sensors, pressure sensors.
- Application: Monitor machinery for early signs of wear and tear. Real-time data helps predict failures before they occur, reducing downtime and maintenance costs.
2. Environmental Monitoring in Oil & Gas
- Sensors Used: Pressure sensors, gas detection sensors, temperature sensors.
- Application: Track pipeline pressure, detect gas leaks, and monitor environmental conditions to ensure safety and regulatory compliance in remote oil fields and refineries.
3. Asset Tracking in Logistics and Warehousing
- Sensors Used: Asset trackers, open/close door sensors, temperature and humidity sensors.
- Application: Track the movement and condition of assets, monitor storage conditions, and ensure inventory remains within specified environmental parameters.
4. Temperature and Humidity Control in Cold Storage
- Sensors Used: Low-temperature sensors, humidity sensors, water detection sensors.
- Application: Maintain optimal conditions in refrigeration units and freezers to prevent spoilage of perishable goods and ensure compliance with safety standards.
5. Energy Management in Smart Buildings
- Sensors Used: AC current meters, voltage sensors, motion sensors, smart thermostats.
- Application: Monitor energy consumption, automate lighting and HVAC systems based on occupancy, and identify opportunities for energy savings.
6. Precision Agriculture and Greenhouse Monitoring
- Sensors Used: Soil moisture sensors, PAR light meters, temperature and humidity sensors, CO₂ sensors.
- Application: Optimize irrigation, monitor plant growth conditions, and automate climate control in greenhouses to improve crop yields and resource efficiency.
7. Air Quality Monitoring in Industrial Facilities
- Sensors Used: Air quality sensors (CO₂, PM2.5, H₂S), temperature sensors, motion sensors.
- Application: Maintain safe working conditions by monitoring indoor air quality, detecting harmful gases, and ensuring proper ventilation in manufacturing plants.
8. Water Leak Detection in Data Centers
- Sensors Used: Water detection sensors, differential air pressure sensors, duct temperature sensors.
- Application: Protect critical infrastructure by detecting leaks early, monitoring airflow, and ensuring cooling systems operate effectively.
9. Process Automation in Food & Beverage Processing
- Sensors Used: Temperature sensors, pressure sensors, vibration sensors, pulse counters.
- Application: Automate production line processes, ensure quality control, and monitor equipment performance to maintain efficiency and compliance.
Industrial wireless sensors provide the versatility, reliability, and scalability needed to address these and many other use cases. By enabling real-time monitoring, automation, and predictive insights, they empower industries to optimize operations, enhance safety, and reduce costs.
- Enterprise AA-battery powered: Our most popular type is ideal for typical commercial & enterprise environments, such as server rooms. A 1,200+ ft. range readily covers most facilities.
- Commercial CC-battery powered: Compact sensor is great for space-restricted areas such as control cabinets or cold storage.
- Industrial: Sensor's weatherproof, NEMA-rated enclosure withstands demanding indoor/outdoor use, e.g., warehouses & production facilities.
Connection Type | Wireless | ||
---|---|---|---|
Sensor Type | Commercial (CC Battery) | Enterprise (AA Battery) | Industrial |
Sensor Housing Dimensions1 |
2.0" (50.8 mm) Width 0.875" (22.225 mm) Height 1.125" (28.575 mm) Depth |
4.375" (111.125 mm) Width 2.470" (62.738 mm) Height 1.111" (28.219 mm) Depth |
3.701" (94.0 mm) Width 2.316" (58.84 mm) Height 1.378" (35.0 mm) Depth |
Gateway Required? | Yes | Yes | Yes |
Range2 | 1200+ Feet 12+ Walls |
1200+ Feet 12+ Walls |
1200+ Feet 12+ Walls |
Battery Required? | Yes Coin Cell (CR123) |
Yes Two AA's |
Yes 1800mAH Industrial |
Battery Life3 | Up to 2 Years | Up to 10 Years | Up to 5 Years |
Internet Required for Data Transmission?4 | No | No | No |
Outdoor Use or Wet Conditions? | No | No | Yes (IP65 Nema Rated Housing) |
Works with Other ioX-Connect Sensors? | Yes | Yes | Yes |
1Dimensions for standard housing sizes. For sensors in non-typical housings, please refer to their data sheets.
2Actual range may vary depending on environment.
3Battery life is determined by sensor reporting frequency and other variables.
4This is transmission from sensor to gateway. All gateways will need active connection for transmission to ioX-Connect. Gateway transmission can be Ethernet or Cellular.
Commercial Sensor Enclosure:
Enterprise Sensor Enclosure:
Industrial Sensor Enclosure:
Your all-in-one wireless monitoring solution
Please reach out to us at: sales@iox-connect.com if you have any additional questions that are not addressed below.
ioX-Connect's Wireless Sensor communication can reach 2,000+ feet through 12+ walls non-line-of-sight.
You can connect up to 50 different ioX Wireless Sensors to 1 gateway. Gateways can also serve as range extenders if you have a big site where sensors will be installed more than 1,000 ft apart.
The life span of the battery is dependent on several factors, including:
- How frequently does the sensor transmit data (Heartbeat)
- How far the sensor is from the wireless gateway
- The obstructions that can cause difficulty in sending data (farther distance and obstructions require that the radio operate at longer intervals to send and receive data)
ioX-Connect Sensors and Gateways provide automated data logging. Our sensors can store up to 4,000 messages if the gateway connection is lost (non-volatile flash, persists through the power cycle). For 10-minute Heartbeat settings, this accounts for approximately 22 days of messages or readings. For 2-hour Heartbeat settings, our sensors can log up to 266 days of readings.
Plus, our gateways can save up to 50,000 sensor messages if its connection is lost. Our sensors and gateways can log all this data before sending it to the ioX-Connect platform—our sensor management and monitoring software—for cloud storage, trending, and analysis.
ioX-Connect wireless products use Encrypt-RF bank-level security, featuring a 256-bit exchange to establish a globally unique key and an AES-128 CTR for all data messages. Security is maintained at all communication points from sensor to gateway, gateway to software, and back again.
ioX-Connect's standard wireless products use several features to help protect sensor data in transit. The proprietary sensor protocol uses very low transmit power and requires specialized radio equipment to operate. Typical wireless devices that run on non-proprietary communication protocols (Wi-Fi, Bluetooth, Zigbee) operate using different frequency bands, so you can't use them to eavesdrop on the radio communications from the ioX-Connect family of sensors. In addition, we use a robust packet tampering evaluation routine to ensure that traffic isn't altered between the sensors and the gateways. This enables us to check for well-formed data packets that only originate from ioX-Connect enabled devices. We have algorithms that protect against spoofing and re-transmission of wireless data packets to safeguard data further.
Absolutely! This is what sets ioX-Connect apart from all other IoT solutions out there. ioX-Connect's Analytics module allows you to combine data from different sources not just sensors to create cross functional reports, analyze and trend sensor data, interact with your historical data and collaborate across departments thereby giving you more insights into your business/operations.
Yes. The ioX-Connect platform can be fed with data from external sensors provided we can retrieve the external sensor data through some service like an API. Please reach out to us at: sales@iox-connect.com for more detail on integration capabilities.
Our Products and Services
We're here to help, do not hesitate to reach out to us by scheduling a quick call with one of our consultants.
Contact Us
Our customer service representative helps you to understand what we offer for your business goals.